PREMIUM, STRUCTURAL, & INDUSTRIAL GRADES, SHEET GOODS, FURNITURE, FENCING, DECKING, RAILING & SIGNAGE
HOME | ABOUT US | CONTACT US
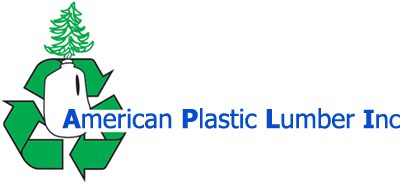
CELEBRATING 25 YEARS
FREQUENTLY ASKED QUESTIONS
If you can’t find the answer to your question here, please contact us and we will do our best to provide answers or specific technical data to assist you.
Distinctions between composite lumber types
Material warranties can vary greatly depending upon the raw material formulation of the product and historical durability. In residential and commercial installations most composite products offer a 5-25 year, with some up to a limited 50 year relative to integrity, staining, fading, mold and mildew.
The most common are wood composites that include a host of products similar to Timbertech, Trex and Fiberon that provide a broad choice attractive finishes, strengths and warranties.
Formulations may include a combination of 40-50% Polyethylene and 50-69% wood fiber. Typically reclaimed grocery bags and stretch film combined with furniture manufacturers wood shavings and recycled wood pallets.
Poly styrene formulations similar to Azek and PVC products have no wood byproducts and typically are used for exterior trim, decking and railing also offered in a host of attractive colors and finishes.
Typically wood composite and styrene formulations are not recommended for structural applications.
Plastic Lumber composites also can be produced from numerous recycled materials such as milk jugs, car bumpers or grocery bags and shrink wrap. Typically high density polyethylene (HDPE) or low density polyethylene (LDPE) respectively.
Plastic Lumber formulations typically include additives such as anti-foaming agents to reduce interior voids, ultraviolet inhibitors to protect product from excessive sunlight degradation and enhance color stability.
Structural plastic lumber may also include formulations with varying percentages of fiberglass or minerals in order to achieve additional flexural strength and reduce expansion and contraction caused by temperature variations.
Structural Plastic Lumber can be engineered for utilization in post, beam, joist, girder, fender, boardwalk, pier, railing and deck applications for wood replacement.
Plastic Lumber may be embedded directly in soil, rock as well as wet set into concrete or saltwater without compromising warranty conditions.
Typically plastic lumber products provide a limited warranty for 50 years in residential, commercial and structural installations. Splintering, cracking, mold, and insects do not compromise plastic lumber products.
Information contained herein is generalized and subject to review by consumer for individual products, and may become inaccurate as product improvements, formulations and warranties may be altered over time.
How to Order
Signed estimates are required as part of our operations processing, essential for order verification and to ensure order accuracy. Thank you for your understanding. We very much appreciate your business.
To turn your estimate into an order, the process is simple:
- Send your Approved and SIGNED estimate
- All orders are custom and must be prepaid. Payment is accepted via the following methods:
- Check (send scanned/photocopy of your check prior to mailing to expedite) or
- Wire transfer (send proof of wire transfer transaction to expedite) or
- Direct deposit, Wells Fargo Bank (send proof of ACH to expedite)
Should you wish to send payment via bank deposit or wire, our accounting department will send you the information and instructions.
Cancellation & Return Policy
At American Plastic Lumber, we do our best to ensure you are quoted the appropriate product and satisfied with your purchase, however: All sales are final. Orders cancelled after placement, during production or post-production require management’s review and may be subject to a 50% Restocking Fee for lumber or sheet goods and 60% on furniture or unassembled products. Please check your item(s) as soon as they arrive and contact us in writing immediately if order is incorrect or damaged, with notice of damage noted on freight bill before signing for delivery. Photos of damaged goods is required.
All returns or cancellations are subject to approval and require a Return Authorization (RA) number in advance. Return shipping costs are the responsibility of the purchaser unless damages occurred in transit.
Expansion & Contraction
It is recommended that an engineer review the design prior to installation in order to comply with technical specifications provided, relative to the expansion and contraction characteristics of the material(s), as well as the fastening method(s) used.
Recommendations for Installation:
- Pre-drill and oversize all holes in order to allow for the expansion and contraction of the material.
- Use good quality stainless steel or galvanized hardware.
- Do not over tighten the hardware–the material has to be able to move.
Maintenance or Cleaning
ADDITIONAL CLEANING INFO
Cleaning may be done with a power washer, taking caution to ensure nozzle does not get too close to lumber or using a brush with a mild soap/cleanser and water.
What is plastic lumber made of?
How long does it take for you to ship it to me?
Does plastic lumber really cost that much more?
Are the boards slippery?
Can I paint or glue it?
What type of tools do I need?
*See installation guidelines span charts: available upon request.
Will it stain from food spills, bird or animal droppings?
What about really hot or really cold climates?
When pre-drilling, oversize holes in order to allow for expansion and contraction, allow gaps at each board end in cold installations. Expansion and contraction must be taken into consideration in the design stage to avoid installation issues over time.
*Please see our technical data: page for more details available upon request
Largest selections of colors, sizes & grades available.
American Plastic Lumber has provided maintenance-free recycled plastic lumber products throughout the world for over a quarter century.
American Plastic Lumber, Inc
P.O. Box 514
Shingle Springs, CA 95682
Toll Free: (877) 677-7701
Local: (530) 677-7700
Fax: (530) 677-6718
Email: sales@aplinc.us